SCI-Arc Students Team with ‘Operation Protect the Heroes’ for Frontline Workers
Spurred by the nation’s shortage of Personal Protective Equipment (PPE) for underserved hospitals and medical workers on the frontline of the COVID-19 pandemic, SCI-Arc students Asya Nur Celik (B.Arch ’21 and Burak Celik (M.Arch 2 ’21), along with Ege Yener, formed 3D Collaborative Network and connected with “Operation Protect the Heroes,” an initiative founded by producer Austin Sepulveda (Looks That Kill) and Voltage Pictures to produce and assemble thousands of urgently needed face shields.
The face shields utilize a design created by 3D Printing Design Group Budmen which has been certified by the National Institute of Health and LA Mayor Eric Garcetti. To date over 15,000 face shields have been printed and distributed, by a liquid mold injector and over 300 volunteers.
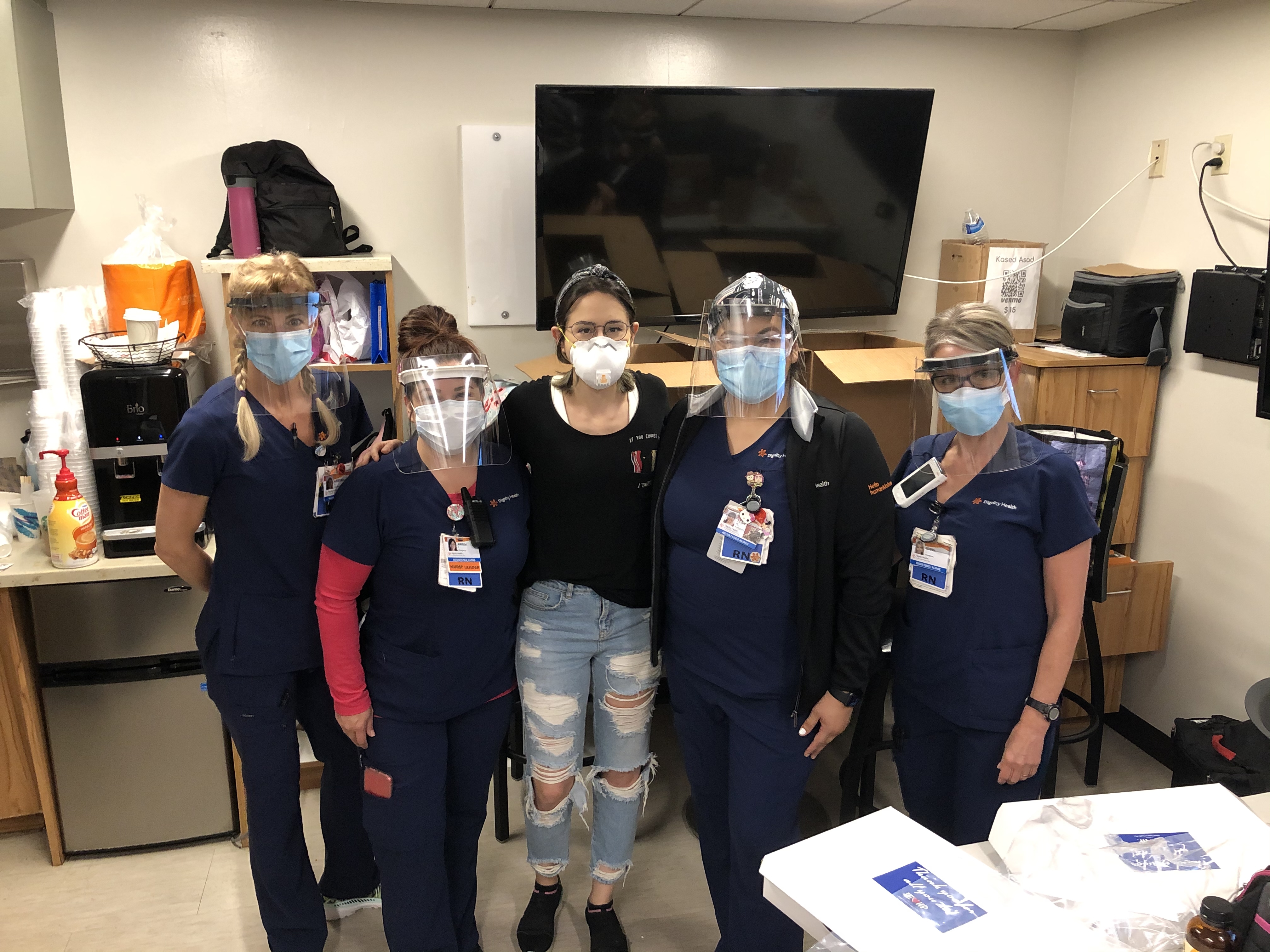
SCI-Arc spoke with Celik, Nur Celik, Yener, and Sepulveda about their efforts via Zoom, after which we were given a virtual tour of their impressive assembly and distribution facility.
Who are each of you, and what has been your involvement with SCI-Arc?
Asya: I am in my fifth year of the B.Arch program so I’ll be graduating next year.
Burak: I just finished my first year of the M.Arch 2 program, and next year will be my final year.
Austin: I'm Austin. I'm a film producer and I have nothing to do with architecture or SCI-Arc [laughs].
How did you become involved in this project?
Austin: I produced a movie in upstate New York with a production company [American High]. They started doing what we're doing down here, manufacturing and distributing face shields to hospital workers and frontline workers. And they partnered with an architectural firm up there called Budmen, whose design we are using now. Budmen, I believe, put us in touch with SCI-Arc and Asya, Burak, and I got on the phone—we just figured that there'd be a way to join forces, and the rest is history.
Asya: Yeah, Ege, Burak, and I started the 3D Collaborative Network, and began collecting 3D designers.
Burak: I was also a volunteer, so I thought we could start an initiative here too. Ege and I have known each other for years, and he started doing this in San Francisco himself. Asya and I then expanded and joined in San Francisco as well.
From there, how did the PPE project get started?
Asya: When the COVID pandemic started, we wanted to do something more than just sitting home. We wanted to help, but while of course being careful. I have friends in the medical field that gave me this idea, and I started sending emails to several of my friends. I reached out to Burak and he in turn reached out to Ege. Through that, we started reaching out to designers and architects we know—mainly the SCI-Arc community, because we were students there and we know who has 3D printers.
We initially started printing out a different design but wanted to collaborate with SCI-Arc, who helped us with a new file that was approved by NIH. For logistics and drop-off, pick-up point, or finding materials for PPG, Rodney [Rojas, SCI-Arc Shop Director] became our contact. Then Austin started communicating with us, and we became a team.
Ege: Burak and I have known each other for four years and talk every day. I received a call from him saying, "We're sitting at home doing nothing. How can we do this? How can we help?" Once Asya joined us, we started talking about this amazing idea; we just needed people to pull it off.
We started reaching out to our communities, and I think because it's been a volunteer effort, people just wanted to participate. It was amazing how fast we grew. And mostly it was SCI-Arc students first, because Asya and Burak were able to get really fast responses, which was a really great help. Inspired by them, I reached out to my faculty at CCA, and faculty and students got really interested, so we started a group here also. And they shipped out our first batch of masks, 100 of them to us here, San Francisco. They were producing more, more effectively.
Austin: Led by Russ Taylor and Paul Barney, we’ve now turned Brian Bohner’s Fat Eye Studios into an assembly hub for the face shields. Our collaboration grew, and we established bigger teams in different cities—from three people to 300. It's been just amazing.
What was the process of developing and creating the face shields themselves? With whom did you collaborate and what were each of your roles in that collaboration?
Asya: The face shields were originally from a design approved in Europe and North America, but later on USC was able to share their files, which were also approved by the Los Angeles mayor's office. Rodney shared it with us, and we changed our files. It was at that point Austin joined our team, who was a big help when it came to logistics and assembly center and materials and finding out more and producing faster masks.
Austin: When I joined in, these guys already had a vast network of printers lined up and ready, which was a huge head start. I was finding 2, 3, 4, 5 people at a time, and they already had 75 by the time I joined. And we knew that with the 3D printers, we could be printing right away with no lag time. While they were doing that, I realized that where I could fit into the puzzle was, one, having a hub—actually having these things assembled. They take about two hours per mask to print, and that doesn't even include the assembly of the actual mask.
And you have everything so decentralized, you can't quality control, you can't sanitize. The hub allowed us to take a decentralized network and centralize it. And then from that point, it was easy to say, "Okay, now we can assemble these. Now we can get these out to the contacts that they had already set up from the hospitals." 3D printing was the initial, first way to do it because it was something that could be done instantaneously. There wasn't any upstart money necessary and there were no upstart costs.
We've now moved the majority of our productions toward liquid mold injecting. Where a 3D printer might take two hours, a liquid mold injector takes 40 seconds. At this point, we can produce thousands a week, whereas before we were hoping to do a couple hundred.
That's amazing. Can you explain how you worked out the process from production to distribution?
Austin: That part of the process has been really good. We're now using more of a distribution drop-shipping type business, versus a purely manufacturing one; from soup to nuts. And at SCI-Arc, they were able to find PPG plastic at a cost that was less than half of what we were originally paying.
We've raised a lot of money privately thus far, and have some really great partners. A company called Voltage Pictures, who has a couple of their employees right now on assembly, have been hugely helpful from a fundraising standpoint, and just oversight as a whole. Pierre Henry was instrumental in the early stages of the first money in, getting the ball rolling, which is the hardest part. He was one of the people that was there and oversight throughout. Robert Downey Jr. and Susan Downey's nonprofit [Random Act Funding] and Kent Seton of the Edward Charles Foundation have been our anchor donor and fiscal sponsor—which allows us to receive funds that can then be tax deductible.
Burak and Ege, would you like to speak to each of your individual roles?
Ege: Well we have been collaborating labs here in San Francisco, such as Future Cities Labs, led by Jason Kelly Johnson, who is also leading the digital craft lab in CCA.
We have also been growing in terms of involving people from other projects. We established a website called PPESF.org, through which we were able to receive donations and people started to reach out to us. We have been doing these deliveries to UCSF [University of California San Francisco] as a major donation. But then smaller facilities started to reach out to us, local facilities, from dog hospitals to elder care. And these people need like 50, 20 masks a week, so we shifted our efforts while still providing to UCSF. Which then grew into much more of a collaborative effort, with people donating their time and space for pickup and delivery, sanitization, production, and more.
Burak: In terms of the social media element, we created an open source Google Drive file that includes all the continuously updated 3D files and a doc sheet for people to sign up and follow the paths that we are following, like hospital names and numbers. This is how people are also connected with the network, which has now grown to almost 80 people.
What have your experiences been like making and then distributing the face shields? You actually did go to the hospital and distribute a few of them yourself, correct?
Asya: It's been amazing. I was personally in charge of finding hospitals, because I have a lot of friends in this field. When you drop off [the shields], the feeling of warmth and happiness you get from the healthcare workers in their hardest times, and hearing things like, "Oh, we feel so much safer with these," has been amazing. I'm just glad that we can help in some without leaving our home, and rather than just sitting home; being able to do something to go to our most vulnerable.
And once we fill those orders, we're hoping to help essential workers all around California to include supermarkets or trash collectors or cleaners or any and all people who can't work from home right now.
What has the response been like to this project?
Asya: Extremely positive. A lot of people have been messaging us and saying, "Thank you for starting this out." But it wouldn't have been possible without every single person in distribution. It's just been a big team of people always just having each other's back—I think that's what makes it amazing. How you see the community gets together in the hardest of times, and how in normal conditions, maybe we all wouldn’t have met or worked together. No matter what kind of field you're from or where you're from, community gets together and tries to make a thing that we can use as a force of good.
Austin: It feels like we're doing something so small and insignificant compared to what they're doing on a daily basis, so it's nice to give them something that helps them do their jobs more safely.
It's very exciting that you have been able to make this happen. Finally, what are your plans for this project moving forward?
Austin: I think we’ll just keep going until someone says stop.
Asya: That's definitely what we're aiming for. And hopefully in the future, we want to use this network into something bigger and more continuous, and maybe even after COVID over—because we have an amazing network and such hardworking members on our team. We'll see wherever the help is needed. Maybe we'll be there.
This was fantastic. Thank you all for speaking with us!
Group: Thank you.